Quality Policy
Mahalaxmi Steel Centre continually improves the effectiveness of the quality management system (QMS) and sets quality objectives and work plans. Moreover, Weare committed to upgrading the capabilities of its technical and administrative staff through formal training and continuous technical quality awareness.
We have achieved high quality through the professional competence of the personnel, high working motivation, and a service-minded attitude. Every single employee of Mahalaxmi Steel Centre is responsible for the quality of his/her work.
All our products are tested in accordance with internationally recognized standards or our own more stringent internal test procedures, which are developed considering the harsh field conditions. In addition to this, we also offer specific testing to our client’s requirements.
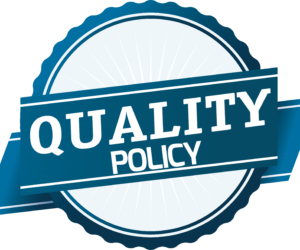
RAW MATERIAL TESTING
All the material used for the Manufacturing of fittings and other fabrication jobs is tested for chemical & mechanical properties. The Results are confirmed to meet the original material requirement before processing. We are using measuring equipment calibrated by Govt. approved calibration Agencies.
DIMENSIONAL INSPECTION
All types of Flanges and fittings are checked for dimensional accuracy from raw material stage to in-process & final product delivery by using calibrated measuring instruments.
MATERIAL TRACEABILITY
All the material used for the Manufacturing of fittings, valves, and other fabrication jobs are identified & fully traceable from raw material stage to the final product.
SOME SPECIAL TEST ON REQUEST OF CLINTS:-
PNEUMATIC/GAS TEST
ALL COMPRESSOR AND THREADED FITTINGS and valves are subjected to Pneumatic test at 150psi air pressure and 2000psi Nitrogen pressure. Pneumatic/Gas test is carried out after hydro testing and complete drying of the items following Hydro-Test.
Helium Gas Test (HG-TEST) can be offered on request.
PRESSURE CYCLE TEST
All fittings and valves are tested for pressure cycle test where pressure surges from Opsi to 5000psi. The test is conducted at the rate of 25 to 45 cycles per minute with the digital counter. The client can specify the number of cycles and conditions of the test.
TEMPERATURE TEST ON REQUEST
fittings and valves are heated to temperature up to 350oC for one complete cycle of 4 hours. After that valves are again subjected to Hydro, Pneumatic, and Pressure cyclic test for no leakage. All the above tests are certified by our own Quality control department and can be witnessed by the client or third-party inspection company of the client’s choice.
VIBRATION TEST
fittings and valves are tested for severe vibration under impulse pressure for no leakage
QUALITY ASSURANCE PLAN FOR PIPES | ||
Sr. No. | Stages Of Inspection | Inspection By Third Party /Client’s Representative |
I. | RAW MATERIAL IDENTIFICATION and Check testing | Putting stamps on identified Pipes and Samples and sending samples to Govt. approved Lab. |
Dimensional & visual checking | At random or as desired by third party Inspector / By client’s representative & verification of Manufacturer’s test Certificate | |
Chemical Analysis | Witnessing of Tests & verification of Test Report | |
Physical – Tensile Test & Micro Test | Witnessing of Tests & verification of Test Report | |
II. | Acceptance of Materials | Putting final identification mark on Pipes and issuing of Dispatch Clearance Certificate |
QUALITY ASSURANCE PLAN FOR WELDED PIPES | ||
Sr. No. | Stages Of Inspection | Inspection By Third Party /Client’s Representative |
I. | RAW MATERIAL IDENTIFICATION and Check testing | Putting Stamps on identified Raw materials and samples and sending samples to Govt. approved Lab |
Dimensional & Visual checking | At random or as desired by Third Party Inspector / By client’s representative | |
Chemical Analysis | Witnessing of Tests & Verification of Test Report | |
Physical – Tensile Test & Micro Test | Witnessing of Tests & Verification of Test Report | |
Stamp Transferring | Only if test conforms to your specification | |
II. | Submission of : WPS | Approved by Third Party / Client. |
PQR | Witnessed by Third Party Client | |
WELDERS PERFORMANCE TEST | Verification of Approved Lab Test Certificate | |
Filler Wire / Welding Rod | Chemical Analysis to be carried out /M.T.C. to be verified | |
III. | D. P. Test (a) 100 % Root Run (b) 100 % Final Weld | To be witnessed by Inspector |
Radiographic Examination for 10% Weld joints or as desired by Customer / Inspector | X- Ray Films and Test Reported to be verified | |
Hydro Test (On Random samples) | Test reports to be verified | |
Pickling and Passivation | Report shall be submitted to Inspector | |
IV. | Tensile Test on the welded portion, Micro Test on The weld effected area | To be witnessed and Reports to be verified |
Flattening Test of finished pipe | To be witnessed and Reports to be verified | |
V. | Final Inspection | Dimensional check & Visual Inspection |
VI. | Acceptance of Materials | Putting final acceptance mark on the materials and etching / stenciling and issuing of / dispatch Clearance Certificate |
QUALITY ASSURANCE PLANS FOR 2 HALVES WELDED PIPE FITTINGS FOR STAINLESS STEEL, ALLOY STEEL & CARBON STEEL | ||
Sr. No. | Stages Of Inspection | Inspection By Third Party /Client’s Representative |
I. | RAW MATERIAL : Identification and Check testing | Stamping on identified Raw Materials and samples andsending samples to Govt. approved lab |
II. | DIMENSIONAL & VISUAL CHECKING | At random or as desired by Third party inspector / by client’s Representative |
III. | CHEMICAL ANALYSIS | Witnessing of Tests & Verification of Test Report |
IV. | PHYSICAL : Tensile Test Micro Test | Witnessing of Tests & Verification of Test Report |
V. | STAMP TRANSFERRING TO TEMPLATES | Only if the Tests confirms to order specifications |
VI. | SUBMISSION OF : WPSPQR | Approved by Third Party / Client Witness by Third party client |
VII. | WELDERS PERFORMANCE TEST | Verification of Approved Lab Test Certificates |
VIII. | FILLER WIRE / WELDING ROD | Chemical analysis to be carried out / M.T.C. to be verified |
IX. | D.P.TEST (a) 100 % Root Run(b) 100 % final weld | To be witnessed by Inspector |
X. | RADIOGRAPHIC EXAMINATION FOR 10 % WELD JOINTS OR AS DESIRED BY CUSTOMER / INSPECTOR | X – Ray films and Test Report to be verified |
XI. | Tensile Test on the Welded portion Micro Test on the weld effected area | To be witnessed and reports to be verified |
XII. | HEAT TREATMENT & SOLUTION ANNEALING | As desired by client / Third Party Inspection Agency |
XIII. | PICKLING AND PASSIVATION FOR S.S. | Report shall be submitted to Inspector |
XIV. | SHORT BLASTING, OILING /WARNISHING AND PAINTING FOR A.S. & C.S. | Visual Inspection |
XV. | MARKING | Etching / Punching of size, sch, specn. & heat No. |
XVI. | FINAL INSPECTION | Dimensional check & Visual inspection |
XVII. | ACCEPTANCE OF MATERIALS | Putting final Acceptance Identification Marks and issuing of Dispatch Clearance Certificate. |